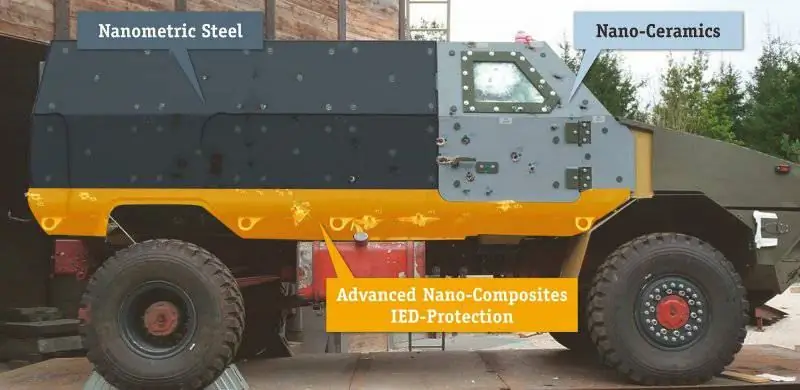
Iveco MPV ใช้โซลูชันการป้องกัน IBD Deisenroth ล่าสุด ซึ่งใช้นาโนเทคโนโลยีเป็นหลัก
เกราะติดตัว: อุปสรรคสุดท้าย
ตัวถังรถหุ้มเกราะยังคงทำจากเหล็กซึ่งมีชุดเกราะเพิ่มเติมติดอยู่ อย่างไรก็ตาม ยิ่งการออกแบบพื้นฐานสามารถให้การป้องกันขีปนาวุธและวัตถุระเบิดได้มากเท่าใด ระดับการป้องกันขั้นสุดท้ายก็จะยิ่งสูงขึ้น นอกจากนี้ แม้จะติดตั้งระบบป้องกันแบบแอ็คทีฟที่ทำลายขีปนาวุธโจมตีแม้ในระยะใกล้ ชิ้นส่วนพลังงานสูงที่เป็นผลสามารถก่อให้เกิดความเสียหายร้ายแรงต่อยานพาหนะ ซึ่งต้องมีการป้องกันขั้นพื้นฐานที่ดีอีกครั้ง
SSAB บริษัทสัญชาติสวีเดนเป็นหนึ่งในผู้เชี่ยวชาญที่มีชื่อเสียงในด้านวัสดุเกราะ และกลุ่มเหล็กกล้า Armox ของ Armox เป็นที่รู้จักไปทั่วโลก ตระกูลนี้มีหกประเภทที่แตกต่างกัน ตัวเลขในการกำหนดเกรดเหล็กบ่งบอกถึงความแข็งของบริเนลโดยเฉลี่ย แม้ว่าความแข็งจะส่งผลโดยตรงต่อการป้องกันขีปนาวุธ แต่จำเป็นต้องมีความเหนียวในการดูดซับพลังงานระเบิด ซึ่งเป็นลักษณะสองประการที่แท้จริงแล้วไม่สามารถอยู่ร่วมกันได้ ความสามารถในการขึ้นรูปทำให้ข้อขัดแย้งนี้รุนแรงขึ้น เนื่องจากโดยทั่วไปแล้วเหล็กกล้าที่มีความแข็งแรงสูงมักมีการขึ้นรูปน้อยกว่าและมักมีปัญหากับความสามารถในการเชื่อม
เมื่อเวลาผ่านไป ลักษณะขีปนาวุธของเหล็ก SSAB ค่อยๆ ดีขึ้น: ในปี 1990 จำเป็นต้องใช้เหล็ก Armox 500T ที่มีความหนา 9 มม. เพื่อหยุดกระสุนปืน M193 / SS92 ที่บินด้วยความเร็ว 937 m / s แต่สิบปีต่อมากับ Armox โลหะผสม 600T ต้องการเพียง 6 เพื่อหยุดมม. อีกสิบปีกับ Armox Advance 4.5 มม. ทำเช่นเดียวกันแม้ว่าตัวเลขจะไม่คุ้มค่าอีกต่อไปเนื่องจากความแข็งเกินมาตราส่วน Brinell! จากเริ่มต้น 70.7 กก. / ตร.ม. SSAB สามารถลดน้ำหนักลงเหลือ 47.1 กก. / ตร.ม. ในสิบปีและลดลงเหลือ 35.3 กก. / ตร.ม. ในทศวรรษหน้า ตามที่ผู้เชี่ยวชาญของ SSAB คาดการณ์ไว้ว่าจะไม่ลดลงอย่างมีนัยสำคัญอีก ตัวเลขที่แท้จริงสำหรับปี 2020 คือ 30 กก. / ตร.ม. แผนก R&D ของบริษัทกำลังทำงานในการปรับปรุงความเหนียวและความสามารถในการขึ้นรูปของวัสดุที่มีอยู่มากกว่าความแข็ง โดยเฉพาะอย่างยิ่งเนื่องจากการระเบิดเป็นภัยคุกคามหลักในปัจจุบัน เหล็กกล้า Armox 440T 420-480 HB Brinell ได้รับการขนานนามว่าเป็นผู้กินพลังงานที่ต้องการ และความเหนียวของมันทำให้ได้รูปทรงต่างๆ ได้ง่าย เช่น ก้นที่มั่นคง แม้แต่เหล็กกล้า Armox 500T ที่แข็งกว่าซึ่งมีความแข็ง 480-540 HB ก็ถือเป็นวัสดุสำหรับป้องกันการระเบิด
ดังที่ได้กล่าวไว้ข้างต้น ลักษณะสำคัญของ Armox Advanced คือความแข็ง ดังนั้น SSAB จึงถือว่าเหล็กชนิดนี้เป็นเซรามิกโดยพฤตินัย ดังนั้น บริษัทจึงไม่แนะนำอย่างยิ่งว่าไม่ควรขึ้นรูปหรือเชื่อม เนื่องจากไม่ควรให้ความร้อนสูงกว่า 100 ° C เพื่อรักษาความแข็ง วิธีการบรรลุระดับการป้องกันและน้ำหนักที่ใกล้เคียงกันในอนาคตด้วยวัสดุที่ขึ้นรูปได้มากขึ้นนั้นเป็นงานที่ยากมากในปัจจุบัน
ในบรรดาเหล็กหุ้มเกราะใหม่ แน่นอนว่าควรสังเกต Super Bainite ซึ่งเปิดตัวในฤดูใบไม้ร่วงปี 2011 พัฒนาโดยห้องปฏิบัติการวิทยาศาสตร์และเทคโนโลยีการป้องกันประเทศ DSTL ของสหราชอาณาจักร เหล็กกล้าชนิดใหม่นี้ผลิตขึ้นที่ Tata Steel UK มันแสดงประสิทธิภาพที่ดีกว่าเหล็กเกราะมาตรฐานมากลักษณะเหล่านี้ไม่เพียงเป็นผลมาจากองค์ประกอบทางเคมีเท่านั้น แต่ยังรวมถึงกระบวนการผลิตอีกด้วย โดยเฉพาะอย่างยิ่งการอบชุบด้วยความร้อนด้วยการทำความเย็นด้วยอากาศและเกลือหลอมเหลว ผลิตภัณฑ์ขั้นสุดท้ายมีประสิทธิภาพการขีปนาวุธเป็นสองเท่าของชุดเกราะที่เป็นเนื้อเดียวกัน
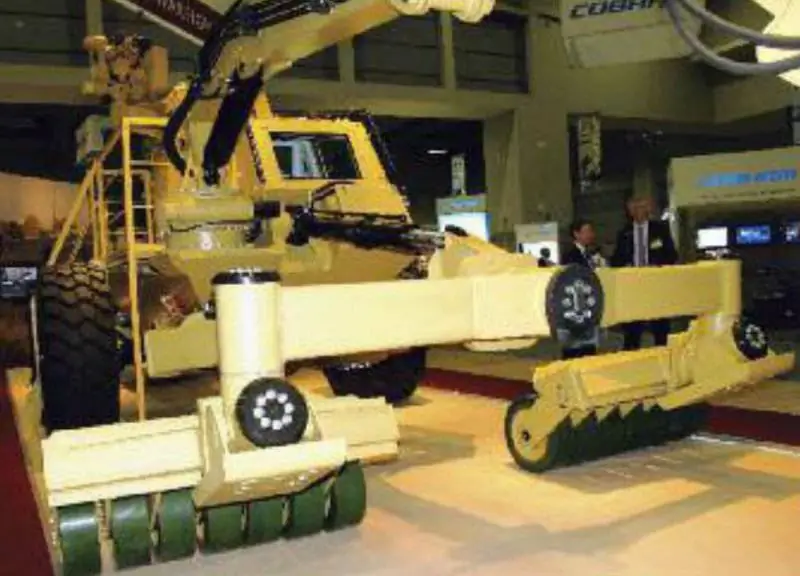
บริษัท Aardvark Perroc ในแอฟริกาใต้ใช้เหล็กกล้า SSAB Armox 500 อย่างกว้างขวางในผลิตภัณฑ์ของตน นี่แสดงให้เห็นว่าแม้แต่เหล็กที่มีความแข็งสูงนี้ก็สามารถดูดซับพลังงานจำนวนมากได้
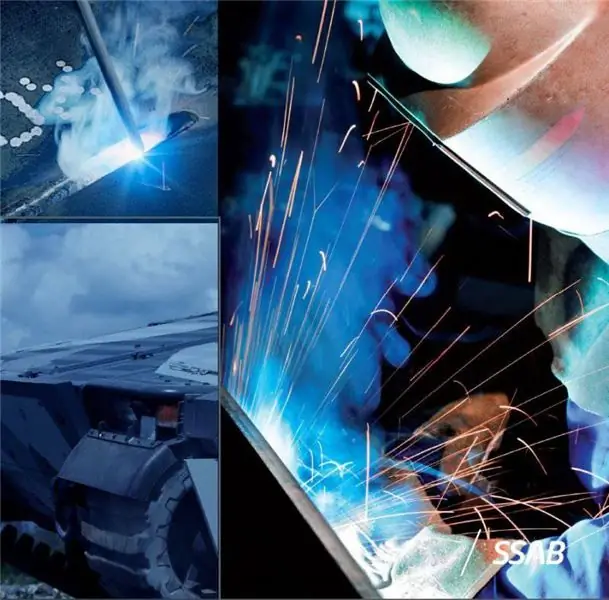
SSAB ผลิตรูปทรงที่ซับซ้อนจากเหล็กกล้า Armox 440T ซึ่งมักเรียกกันว่า "ผู้กินพลังงาน" เหมาะอย่างยิ่งสำหรับโครงสร้างที่สัมผัสกับ IED SSAB กำลังทำงานเพื่อทำให้เกราะเหล็กสามารถขึ้นรูปได้มากขึ้น
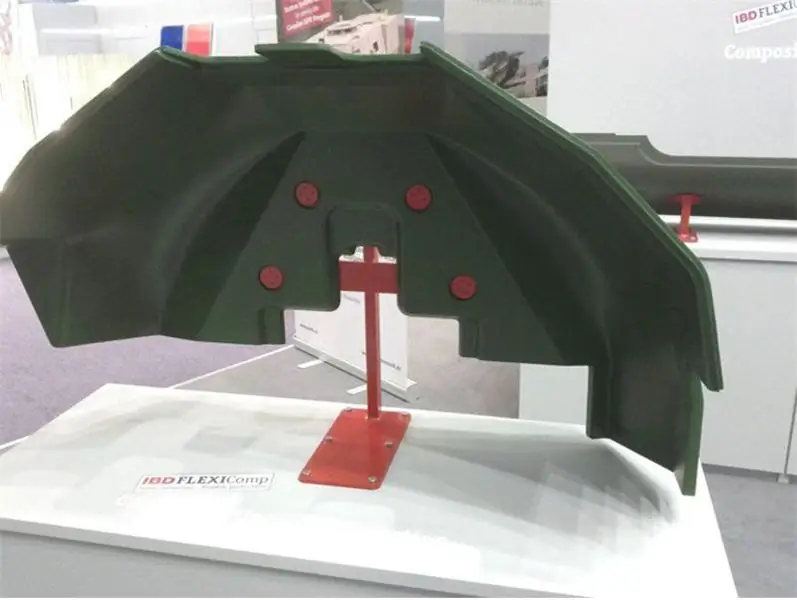
การใช้วัสดุบุผิว IBD FlexiComp ช่วยให้สามารถผลิตส่วนประกอบความปลอดภัยเชิงปริมาตร ลดจำนวนจุดอ่อนในระบบรักษาความปลอดภัยโดยรวม
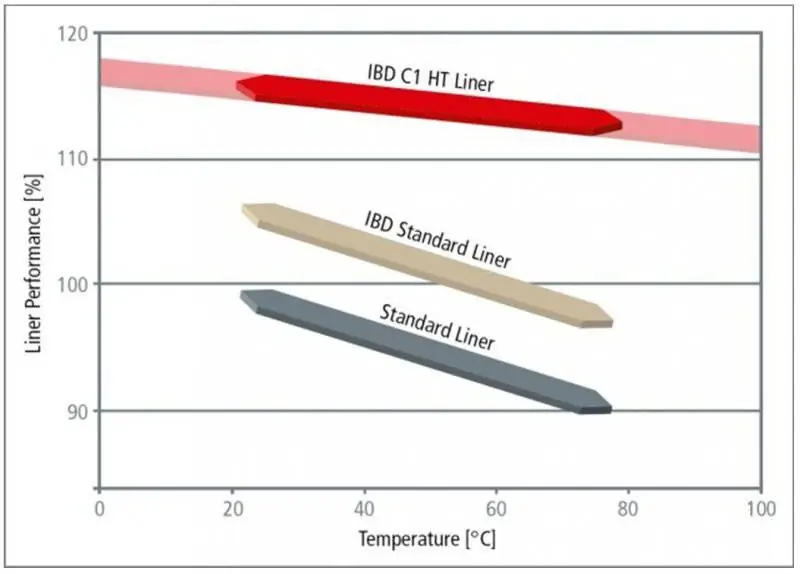
แผนภาพแสดงคุณลักษณะของวัสดุบุผิว IBD ตามหน้าที่ของอุณหภูมิ ผลกระทบของอุณหภูมิสูงเป็นปัญหาสำคัญเมื่อปรับใช้เครื่องจักรในสภาพอากาศร้อน
ในเดือนธันวาคม 2555 Lockheed Martin UK และ University of Surrey ได้ประกาศวิธีการใหม่ที่ง่ายกว่าในการปรับปรุงการป้องกันและความอยู่รอดของยานเกราะ นักวิทยาศาสตร์ได้พัฒนาวิธีการรักษาวัสดุเซรามิกเพื่อปรับปรุงความแข็งแรงในการยึดเกาะของเซรามิกอลูมินาและเซรามิกคาร์ไบด์ซิลิกอนกับพื้นผิวคอมโพสิตซึ่งเพิ่มความแข็งแกร่งของเกราะอย่างมีนัยสำคัญ การติดแผ่นเซรามิกเข้ากับแผ่นรองหลังถือเป็นจุดอ่อนของเทคโนโลยีนี้มาโดยตลอด ผลการวิจัยพบว่าเทคนิคใหม่นี้ช่วยเพิ่มแรงฉุดลาก การทดสอบแสดงให้เห็นว่าเมื่อกระสุนเจาะเกราะขนาด 14.5 มม. ถูกยิงไปที่แผ่นเกราะ กระสุนจะยังคงไม่บุบสลาย
การพัฒนาทางเทคโนโลยียังคงเป็นธุรกิจหลักของ IBD Deisenroth Engineering ในขณะที่โซลูชันแบบพาสซีฟกำลังจ้างงานภายนอกให้กับ Rheinmetall Chempro โดย Rheinmetall Defense 51% ถือหุ้นโดย Rheinmetall Defense และ 49% โดยตระกูล Deisenroth
เมื่อ Dr. Ulf Deisenroth พัฒนาเทคโนโลยีเกราะรุ่นที่สี่สำหรับวัสดุประเภทต่างๆ ภารกิจคือการลดมวลในขณะที่รักษาระดับการป้องกัน หรือในทางกลับกัน เพื่อเพิ่มระดับการป้องกันสำหรับมวลที่กำหนด ในขณะที่เทคโนโลยีใหม่รับประกันการประหยัด กว่า 40% สิ่งเหล่านี้ขึ้นอยู่กับความก้าวหน้าล่าสุดในด้านการป้องกันแบบพาสซีฟที่เกี่ยวข้องกับวัสดุนาโน ซึ่งรวมถึงเซรามิกนาโนคริสตัลไลน์ เหล็กนาโนเมตร และเส้นใยความแข็งแรงสูง ในความร่วมมือกับผู้ผลิตเหล็ก IBD ได้พัฒนาเหล็กไนโตรเจนที่มีความแข็งแรงสูงซึ่งเกือบจะเทียบเท่ากับวัสดุเซรามิกมาตรฐาน เหล็กชนิดใหม่เหล่านี้สามารถนำไปใช้กับองค์ประกอบโครงสร้างได้ ในขณะที่สามารถลดน้ำหนักได้มากกว่านี้หากใช้ในช่วงเริ่มต้นของการออกแบบ สำหรับเส้นใยที่มีความแข็งแรงสูง เช่น IBD C1 HT Liner มีลักษณะที่สูงกว่าเกือบ 20% ไม่เพียงแต่เมื่อเทียบกับซับในมาตรฐาน แต่ยังสูงกว่าเยื่อบุอื่นๆ จาก IBD ถึง 10% การเสื่อมสภาพของพารามิเตอร์ด้วยอุณหภูมิที่เพิ่มขึ้นก็ช้าลงเช่นกัน ซึ่งมีความสำคัญอย่างยิ่งเมื่อพิจารณาจากอุณหภูมิที่สูงมากในสนามรบสมัยใหม่ นอกจากเหล็กกล้าระดับนาโนและนาโนเซรามิกที่ใช้ในเครื่องจักรที่พัฒนาขึ้นใหม่แล้ว IBD ยังได้พัฒนาโซลูชันวัสดุคอมโพสิตใหม่ที่ช่วยให้สามารถผลิตองค์ประกอบที่มีรูปทรงโค้งมนที่ซับซ้อนได้ ซึ่งทำให้สามารถครอบคลุมพื้นที่ป้องกันได้ 100% โดยแทบไม่มีช่องว่างของขีปนาวุธ. สารละลายนี้ใช้โดยเฉพาะในการผลิตชิ้นส่วนด้านล่าง ซึ่งช่องว่างเพียงเล็กน้อยอาจทำให้การป้องกันทั้งหมดลดลง
IBD ยังประสบความสำเร็จในการพัฒนาลามิเนตนาโนคอมโพสิตที่มีความแข็งแรงเพิ่มขึ้นอย่างมากจนสามารถแทนที่ชิ้นส่วนโครงสร้างของเครื่องจักรได้ในขณะเดียวกันก็ทำหน้าที่ป้องกันขีปนาวุธในระดับสูงเนื่องจากความหนาแน่นของพื้นผิวต่ำ น้ำหนักโดยรวมของการป้องกันระดับนี้จึงลดลงอย่างมาก คอมโพสิตเหล่านี้ใช้วัสดุนาโนเทคโนโลยีดังกล่าวจาก IBD กระบวนการยึดเหนี่ยวเฉพาะได้รับการพัฒนาและใช้ในการผลิตลามิเนตนาโนคอมโพสิตของวัสดุโครงสร้างที่เรียกว่า IBD FlexiComp โดยเพิ่มความแข็งแรงของโครงสร้างและประสิทธิภาพของขีปนาวุธ ด้วยความหนาแน่นน้อยกว่า 10% เมื่อเทียบกับลามิเนตมาตรฐาน ทำให้คุณสมบัติความยืดหยุ่นของวัสดุเหล่านี้สูงเป็นสองเท่า ความแข็งแรงสูงนี้ช่วยให้สามารถรวมเข้ากับการออกแบบเครื่องจักรได้ ในขณะที่คุณลักษณะขีปนาวุธช่วยให้สามารถรับมือกับภัยคุกคามระดับสูงได้ ในขณะที่วัสดุ FlexiComp มีศักยภาพในการลดน้ำหนักได้ดี การใช้งานสามารถรวมเป็นสองวิธีที่แตกต่างกัน วิธีการโดยตรงคือการใช้พวกมันเพื่อป้องกันทุ่นระเบิดและ IED เป็นเกราะเพิ่มเติมในซุ้มล้อ บังโคลน เป็นแผ่นทุ่นระเบิดและพื้นภายในที่มีระยะห่าง เมื่อปั้นชิ้นส่วนปริมาตร พวกเขาสามารถแทนที่โซลูชันอื่น ๆ เช่นส่วนประกอบที่ประกอบโดยการเชื่อมหรือโบลต์ วิธีที่สองคือการผสานรวมชิ้นส่วนคอมโพสิต เช่น ฝากระโปรงหน้า ช่องเครื่องยนต์ ประตูท้ายรถ และทางลาด สิ่งเหล่านี้ประกอบเป็นสัดส่วนที่มากของพื้นผิวทั้งหมดของรถ และด้วยเหตุนี้ น้ำหนักที่ลดลงอย่างสมบูรณ์จะมีนัยสำคัญอย่างมาก สำหรับ STANAG 4569 ระดับ 4 การลดน้ำหนักนี้คือ 1500 กก. สำหรับเครื่อง 8x8 (ดูตาราง) ในแง่ของต้นทุนการผลิต กระบวนการที่พัฒนาโดย IBD ช่วยให้สามารถผลิตชิ้นส่วนคอมโพสิตได้โดยไม่ต้องใช้หม้อนึ่งความดัน ซึ่งช่วยประหยัดต้นทุนได้อย่างมาก โดยเฉพาะอย่างยิ่งสำหรับส่วนประกอบขนาดใหญ่ ต้นทุนนั้นเทียบได้กับต้นทุนของส่วนประกอบที่ผลิตโดยใช้เทคโนโลยีมาตรฐาน
ปัจจุบันส่วนประกอบเหล่านี้ผลิตโดย Rheinmetall Chempro ซึ่งมีหน้าที่ควบคุมเทคโนโลยี IBD Deisenroth Engineering พัฒนาเป็นกระบวนการผลิตเพื่อให้ได้ราคาที่แข่งขันได้ พัฒนาโซลูชันเฉพาะทางเพิ่มเติม และติดตามกระบวนการตรวจสอบคุณสมบัติของเครื่องจักร การส่งมอบส่วนประกอบโดยใช้เทคโนโลยีขั้นสูงล่าสุดเริ่มต้นขึ้นในต้นปี 2556 โดยส่วนใหญ่เป็นเครื่องจักร AMPV จาก KMW-Rheinmetall และยานพาหนะที่มีการป้องกันปานกลางจาก Iveco DV-KMW ผู้ผลิตอุปกรณ์ดั้งเดิมมากกว่าหนึ่งโหลทั่วโลกจะได้รับส่วนประกอบในเร็วๆ นี้ ซึ่งจะช่วยให้พวกเขาสามารถลดน้ำหนักของเครื่องจักรได้อย่างแท้จริง ซึ่งจะเป็นการเพิ่มน้ำหนักบรรทุกและลดต้นทุนตลอดอายุการใช้งาน แผนกคุ้มครองของ Rheinmetall กล่าว
กลุ่มผลิตภัณฑ์แบบพาสซีฟของ Rheinmetall Chempro ประกอบด้วยตระกูล Amap (Advanced Modular Armor Protection) เวอร์ชันต่างๆ ครอบครัวนี้ใช้เทคโนโลยีล่าสุดที่พัฒนาโดย IBD โดยทั่วไปแล้ว ผลิตภัณฑ์ Amap จะถูกรวมเข้าด้วยกันเพื่อให้การป้องกันที่ต้องการจากภัยคุกคามที่หลากหลาย ในบรรดาผลิตภัณฑ์ทึบแสงต่างๆ เราเห็นระบบขีปนาวุธ Amap-B ซึ่งให้การป้องกันอาวุธขนาดเล็กและกระสุนขนาดกลาง, การป้องกันทุ่นระเบิด Amap-M, Amap-IED ที่ออกแบบมาเพื่อต่อสู้กับ IED, liners Amap-L ที่ปกป้องห้องต่อสู้ โดยการดูดซับเศษกระสุนทุติยภูมิ, Amap-SC ต่อขีปนาวุธ HEAT และสุดท้ายคือโซลูชัน Amap-X ซึ่งป้องกันภัยคุกคามทั่วไปสำหรับสภาพเมือง
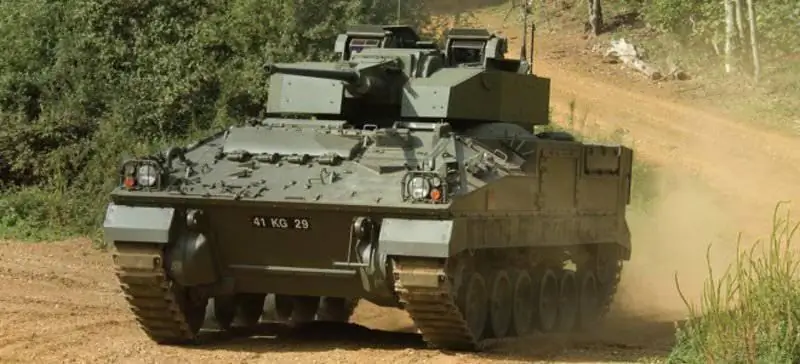
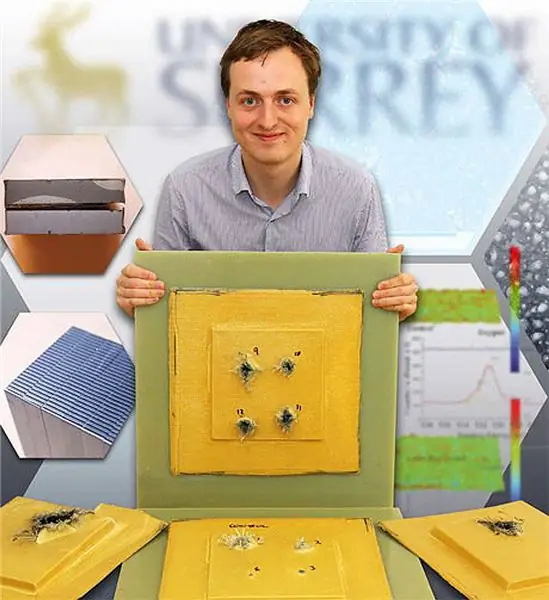
เทคโนโลยีการยึดเกาะแบบใหม่ที่พัฒนาโดย Lockheed Martin UK และ University of Surrey สามารถปรับปรุงการปกป้องยานเกราะได้อย่างมาก เช่น Warrior BMP (ด้านบน)
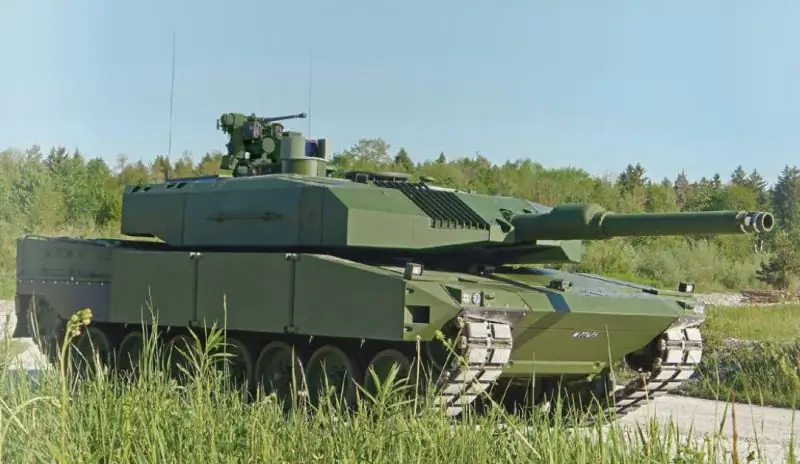
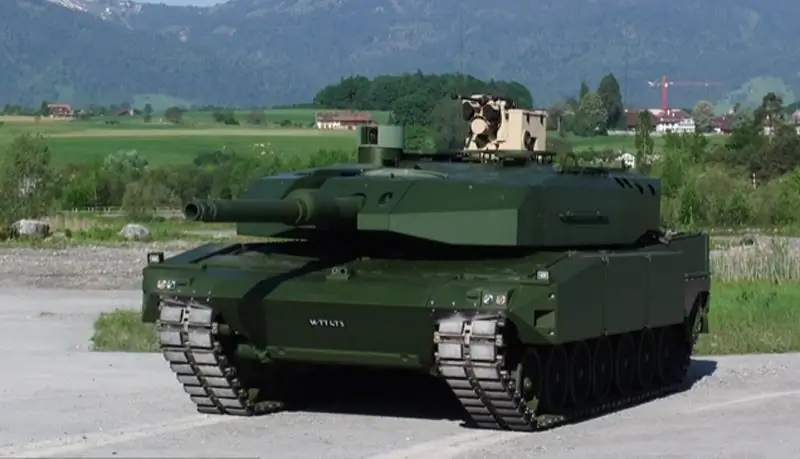
โมดูล SidePro-ATR เพิ่มเติมสำหรับ MBT Leopard
ควรสังเกตว่าภายใน Rheinmetall Group บริษัทอื่นมีส่วนร่วมในการป้องกันแบบพาสซีฟ Rheinmetall Ballistic Protection GmbH ซึ่งได้รับชื่อใหม่เมื่อวันที่ 1 มกราคม 2013 ก่อนหน้านี้เรียกว่า Rheinmetall Verseidag Ballistic Protection GmbHRheinmetall เป็นเจ้าของอย่างเต็มที่ บริษัทนี้เชี่ยวชาญด้านการออกแบบและการผลิตชุดเกราะสำหรับยานพาหนะทางทหารขนาดเล็กที่ใช้วัสดุ เช่น เซรามิก โลหะขั้นสูง และผ้าพิเศษ
แม้ว่า Ruag Defense ยังคงมีโซลูชั่นสำหรับการป้องกันแบบไดนามิก (ชุดเกราะแบบแอคทีฟ-รีแอกทีฟ) ในพอร์ตโฟลิโอ แต่ก็ไม่ได้มองว่าผู้บริโภคเป็นบริษัทที่ล้ำสมัยอีกต่อไปแล้วที่สามารถเพิ่มความอยู่รอดของยานพาหนะขนาดกลางและหนักได้ ในเรื่องนี้ บริษัทสวิสได้หันความสนใจไปที่การแก้ปัญหาแบบพาสซีฟอย่างสมบูรณ์ซึ่งสามารถรับมือกับประจุจลนศาสตร์และรูปทรงได้ ระบบ SidePro-ATR ทำได้ดีกว่าความดุดันของ RPG-7 เนื่องจากสามารถจัดการกับประจุที่มีรูปทรงที่ใช้ในสถานการณ์สมมาตร ในขณะที่รุ่นพื้นฐานรับประกันการป้องกันขีปนาวุธระดับ 5 SidePro-ATR ถูกแสดงต่อสาธารณชนเป็นครั้งแรกในปี 2555 ระบบนี้สามารถปรับขยายได้ ดังนั้นจึงสามารถใช้ได้ทั้งบนยานพาหะติดอาวุธและบนรถถัง ในรุ่นพื้นฐาน มีความหนา 400 มม. และมวลของมันเทียบได้กับมวลของสารละลายปฏิกิริยา (นั่นคือประมาณ 300 กก. / ตร.ม.) ระบบนี้มีคุณสมบัติสำหรับรถถัง Leopard 2A4 ระดับการป้องกันขีปนาวุธสามารถเพิ่มขึ้นอย่างมีนัยสำคัญจนถึงจุดที่ระบบจะทนต่อแรงกระแทกของแกนยาว 120 มม. แม้ว่าจะไม่มีข้อมูลในเรื่องนี้ก็ตาม
ความสามารถในการปรับขนาดของ SidePro-ATR ช่วยให้สามารถใช้ในสถานการณ์การต่อสู้แบบสมมาตรและไม่สมมาตรได้ อีกวิธีหนึ่งในการต่อสู้กับกระสุนจลนศาสตร์และ IED ภายใต้ชื่อ SidePro-KE / IED ได้รับการทดสอบบนยานเกราะลาดตระเวน Fennek ซึ่งให้บริการกับเยอรมนีและเนเธอร์แลนด์ โซลูชันนี้ใช้เซรามิกเป็นหลักเพื่อต่อสู้กับ IED รุ่นแรก ระเบิดริมถนนแบบใหม่ ที่ใช้ในโรงภาพยนตร์หลายแห่ง สร้างชิ้นส่วนความเร็วสูงหลายพันชิ้น ดังนั้นจึงมีความจำเป็นที่จะต้องมีคุณลักษณะการกระทบหลายชั้นที่ดีมาก ตั้งแต่นั้นมา Ruag ได้ปรับปรุงระบบ KE / IED โดยเลิกใช้เซรามิกส์และใช้ถุงหลายชั้นแบบขยายไม่ได้ โซลูชัน SidePro-KE / IED ใหม่ ซึ่งวางจำหน่ายตั้งแต่ปี 2012 มีการป้องกันอาวุธจลนระดับ 4 / ระดับ 5 และประสิทธิภาพการกระแทกที่สูงมาก สมมติว่าแชสซีทำจากเหล็กขีปนาวุธขนาด 7 มม. แผงหน้าปัดขนาด 30 มม. สามารถให้การป้องกันได้เต็มที่ตามที่ต้องการ ด้วยระบบ KE / IED ที่อนุญาตให้เพิ่มน้ำหนักได้น้อยที่สุด ขึ้นอยู่กับประเภทของรถเท่านั้น โซลูชันนี้อยู่ระหว่างรอดำเนินการกับผู้ผลิตหลายราย
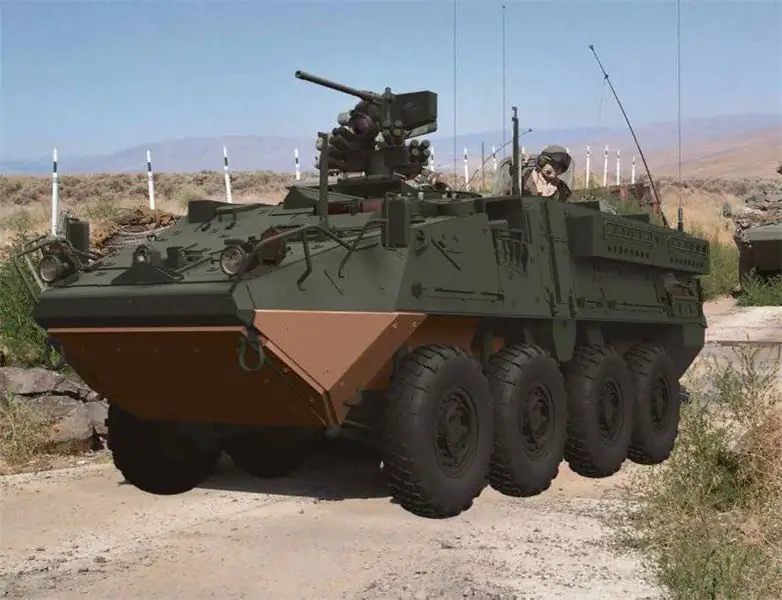
Ruag ได้สรุป SidePro KE / IED แล้ว ภาพตัดต่อแสดงองค์ประกอบของระบบที่ออกแบบมาเพื่อตอบโต้อุปกรณ์ใหม่ที่สร้างชิ้นส่วนหลายชิ้น
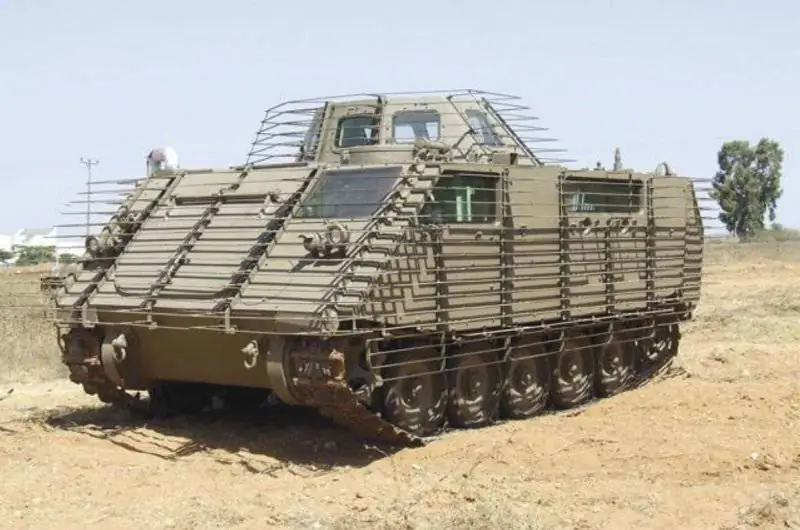
BTR M113 ติดตั้งระบบป้องกัน RPG แบบพาสซีฟ Iron Wall จาก Israel Military Industries ซึ่งรวมเกราะแบบพาสซีฟและแบบตาข่าย
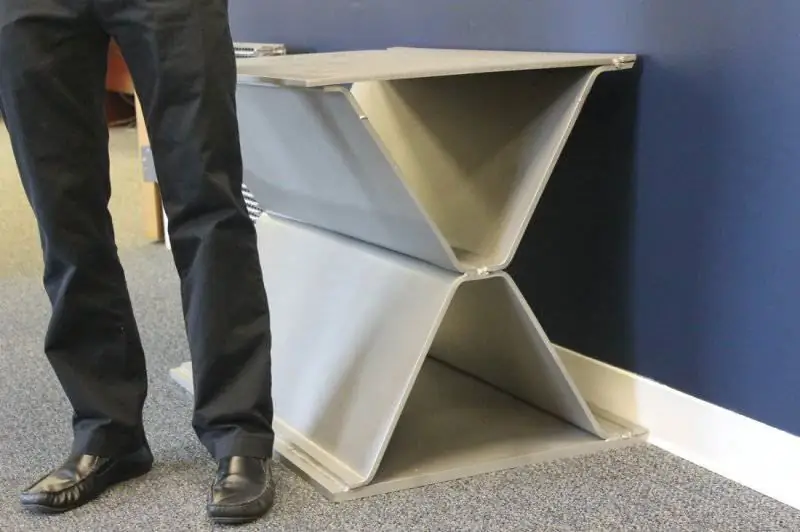
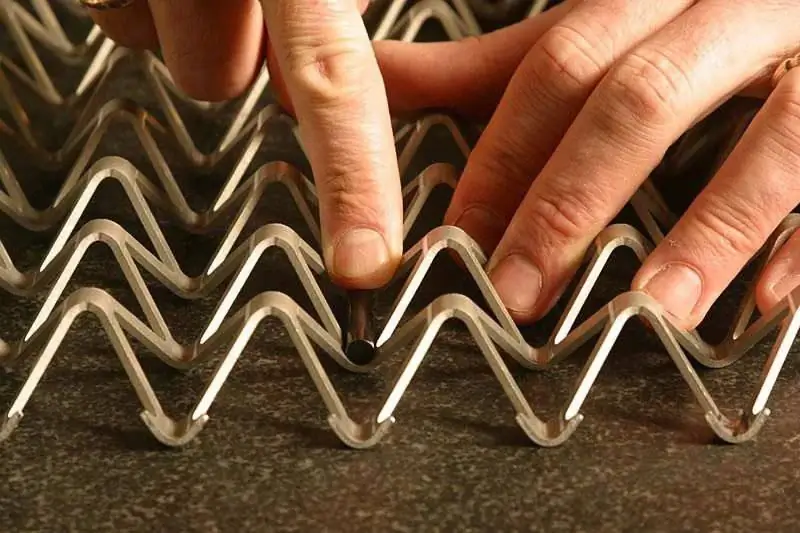
Ceradyne และ Cellular Materials International ได้พัฒนาแผ่นป้องกันด้านล่างโดยใช้ CMI MicroTruss อะลูมิเนียมรังผึ้งที่ดูดซับพลังงานได้มากถึงหนึ่งในสามที่เกิดจากการระเบิด ด้านล่างเป็นภาพระยะใกล้ของวัสดุ MicroTruss
ตัวอย่างการลดน้ำหนักสำหรับเครื่อง 8 x 8 ที่มีส่วนประกอบที่ทำจาก IBD FLEXICOMP
น้ำหนักเป็นกก.
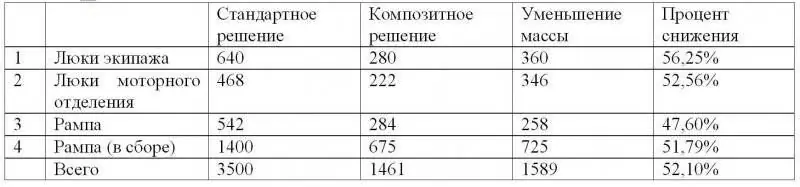
Plasan Sasa ยังคงเป็นหนึ่งในผู้เล่นหลักในอุตสาหกรรมการจองแบบพาสซีฟ ไม่มีรายละเอียดทางเทคโนโลยีในพื้นที่นี้ ในขณะที่บริษัทดำเนินการทั้งในการจองเพิ่มเติมและในอาคารสำเร็จรูป วิธีที่สองเกิดขึ้นพร้อมกับการพัฒนา Mrap จาก Navistar MaxxPro และ M-ATV จาก Oshkosh “สิ่งนี้ช่วยให้เราสามารถเพิ่มการผลิตโดยใช้แรงงานที่ไม่มีทักษะในการเชื่อม เนื่องจากวิธีการแบบเลโก้ของเรานั้นใช้บล็อกที่มีส่วนประกอบทั้งหมดที่สามารถประกอบได้ในเวลาขั้นต่ำ” แหล่งข่าวของบริษัทกล่าว วิศวกรของบริษัทมากกว่าสองร้อยคนของบริษัทกำลังทำงานเกี่ยวกับโซลูชันใหม่ๆ ที่อาจเป็นผลมาจากการเกิดขึ้นของวัสดุใหม่หรือโซลูชันทางเรขาคณิตที่เป็นนวัตกรรมใหม่ แนวทางของระบบยังคงเป็นหัวใจของวงจรการป้องกัน
เมื่อเร็วๆ นี้ IMI ได้พัฒนาโซลูชันแบบพาสซีฟและแบบตอบสนองเพื่อตอบโต้ IED ประเภทล่าสุด รวมถึง "ช็อตคอร์" แบบต่างๆ ของ EFP หรือ SFF (Self Formed Fragmentation) และโมเดล RPG ล่าสุด บริษัทได้เสนอวิธีแก้ปัญหากำแพงเหล็กแบบพาสซีฟโดยใช้โลหะและวัสดุผสมที่เสริมด้วยเกราะตาข่าย ความหนาอาจแตกต่างกันระหว่าง 110 ถึง 150 มม. และน้ำหนักระหว่าง 200 ถึง 230 กก. / ตร.ม. ทั้งนี้ขึ้นอยู่กับระดับการป้องกันที่ต้องการ Iron Wall กำลังอยู่ระหว่างการทดสอบทางทหารกับกองทัพอิสราเอล
IMI ยังเสนอชุดเกราะตาข่ายเป็นระบบสแตนด์อโลน L-VAS (Light Vehicle Armor System - ระบบเกราะสำหรับยานพาหนะขนาดเล็ก) ได้รับการออกแบบมาเพื่อปกป้องยานพาหนะเช่นผู้ให้บริการรถหุ้มเกราะ เพื่อลดน้ำหนัก ระบบจะขึ้นอยู่กับวัสดุคอมโพสิตและองค์ประกอบปฏิกิริยา ซึ่งหลังมีวัสดุที่มีพลังขั้นต่ำ ซึ่งจะช่วยลดการสูญเสียทางอ้อม และชนิดของวัสดุจะช่วยหลีกเลี่ยงความเสี่ยงที่จะเกิดการระเบิดครั้งที่สองขององค์ประกอบที่อยู่ติดกัน ตาม IMI ระบบ L-VAS ยังป้องกันกระสุนเจาะเกราะ 14.5 มม. และชิ้นส่วนปืนใหญ่ ระบบนี้มีคุณสมบัติครบถ้วนในอิสราเอลสำหรับ M113 APC และมีความถ่วงจำเพาะประมาณ 200 กก. / ตร.ม.
นอกจากนี้ยังมีระบบเบรกวอเตอร์ที่หนักกว่าอีกด้วย เกราะปฏิกิริยานี้ ซึ่งประกอบด้วยโลหะและส่วนประกอบ ได้รับการออกแบบมาเพื่อต่อสู้กับภัยคุกคามหลักสามประการ: RPG, SFF และ EFP IMI ได้ทำการทดสอบอย่างละเอียด และขณะนี้กำลังดำเนินการตามคุณสมบัติเพื่อเริ่มผลิตสารละลายที่มีความหนา 350 - 400 มม. และน้ำหนัก 430 - 450 กก. / ตร.ม. ณ สิ้นปี 2556
Ceradyne เป็นอีกหนึ่งผู้เล่นหลักในการจองแบบพาสซีฟ Mark King ประธานของ Ceradyne กล่าวว่าเหล็กยังคงเป็นวัสดุหลักในธุรกิจการจอง โดยมีเป้าหมายในการปรับปรุงประสิทธิภาพและลดต้นทุน “ในสหรัฐอเมริกา ปัจจัยขับเคลื่อนส่วนใหญ่เป็นต้นทุนในการจัดหายานพาหนะ ไม่ใช่ อายุการใช้งาน และสิ่งนี้ใช้ได้กับการอัพเกรด” คิงกล่าวในการประชุม AUA ปี 2555 ในขณะที่ในสหรัฐอเมริกา เน้นที่ ปริมาณซึ่งทำให้นักพัฒนาระบบป้องกันในยุโรปนำหน้าชาวอเมริกัน อย่างไรก็ตาม คิงเน้นว่าขณะนี้อเมริกากำลังก้าวหน้า โดยเน้นที่การป้องกันใต้ท้องรถป้องกันการระเบิดเป็นหลัก เนื่องจากการป้องกันขีปนาวุธถูกมองว่าเป็นปัญหาที่ได้รับการแก้ไข ความสนใจของกองทัพอเมริกันที่แสดงให้เห็นอีกครั้งในการแก้ปัญหาในการปกป้องส่วนล่างของยานพาหนะเช่น Humvee ($ 20 ล้านสำหรับการพัฒนาเท่านั้น) ได้รับการประเมินในเชิงบวกโดย King Ceradyne เป็นหนึ่งในผู้ที่จะแข่งขันกันเพื่อทำสัญญาเพื่อความทันสมัย ข้อกำหนดนี้ให้การปกป้องสูงสุดพร้อมการลดน้ำหนักอย่างมีนัยสำคัญเพื่อลดผลกระทบต่อประสิทธิภาพของเครื่องจักร
Ceradyne ได้พัฒนาโซลูชัน MicroTruss จาก Cellular Materials International Inc (CMI) วัสดุโลหะผสมอลูมิเนียมที่มีรูพรุนนี้มีความหนาแน่น 58 กก. / ตร.ม. เมื่อเทียบกับความหนาแน่น 112 กก. / ตร.ม. ของสารละลายโลหะเสาหินที่เทียบเท่า สารละลายนี้แตกต่างกันในมุม "V" ของร่างกายเท่ากับ 5 ° ซึ่งเพียงพอต่อการสะท้อนคลื่นระเบิดและมีมวล 300 กก. MicroTruss รับประกันการดูดซึมได้ถึง 30% ของพลังงานการระเบิด ซึ่งไม่เพียงจำกัดผลกระทบต่อแคปซูลลูกเรือ แต่ยังช่วยลดการเคลื่อนที่ในแนวดิ่งของยานพาหนะด้วย Ceradyne ยังมีส่วนร่วมอย่างมากในโปรแกรมการจอง Flyer Gen.2 ซึ่งกำหนดเป้าหมายโครงการกองกำลังปฏิบัติการพิเศษสำหรับ GMV 1.1 เพื่อรักษาความสามารถในการขนส่งภายในเฮลิคอปเตอร์ V-22, CH-47D และ CH-53E เมื่อมวลและความกว้างต้องอยู่ภายในขอบเขตที่กำหนด บริษัทได้พัฒนาชุดอุปกรณ์ที่ให้การป้องกันขีปนาวุธระดับ B6 (.357 Magnum) สำหรับประตูและ หลังคา.
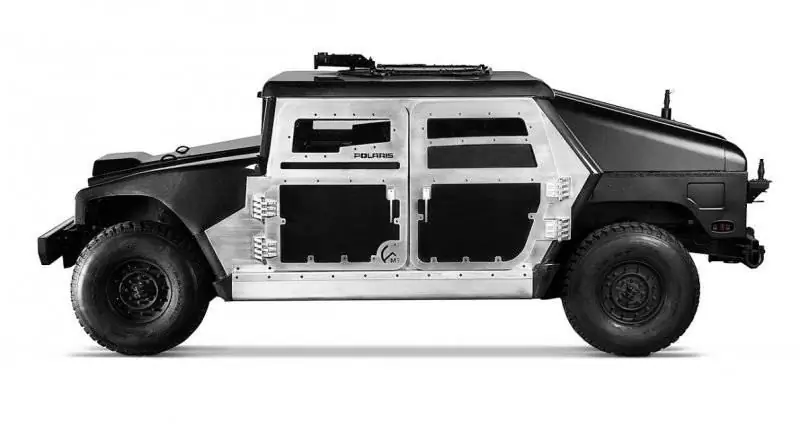
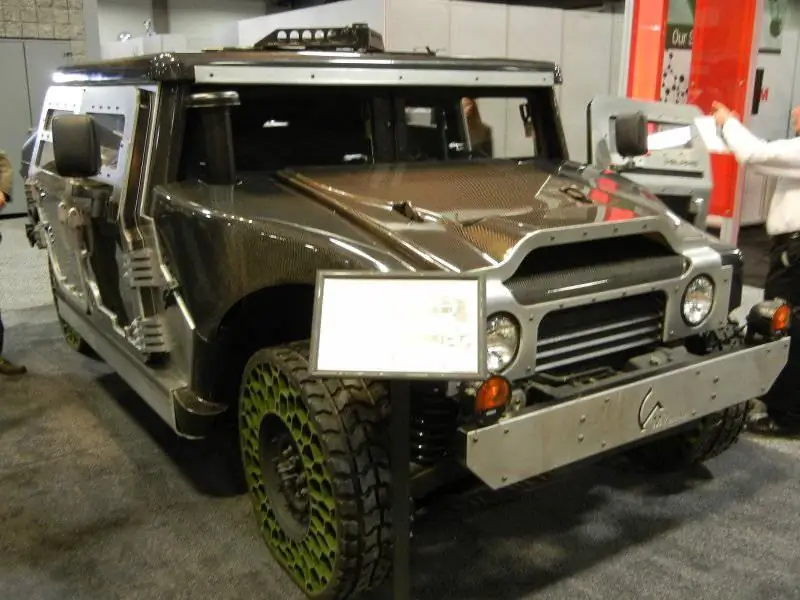
Polaris Defense และ M9 Defense Armor Technology ได้พัฒนาชุดเกราะผสมเหล็กกล้าผสมที่สามารถลดน้ำหนักของ Humvee ได้อย่างมากในขณะที่ยังคงระดับการป้องกันไว้ ต้นแบบในภาพด้านขวามีน้ำหนักเพียง 3400 กก. ซึ่งน้อยกว่า Humvee ที่มีการป้องกันระดับ 3 เกือบ 50%(สังเกตล้อรถด้านล่าง)
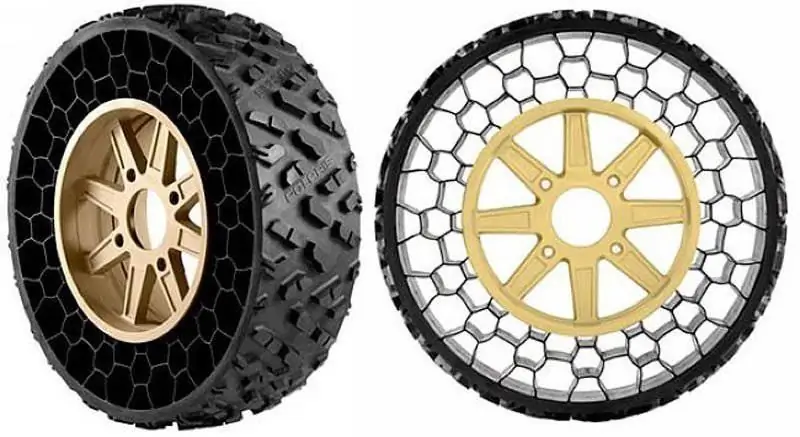
การป้องกันยังเป็นเรื่องการไม่ถูกทิ้งไว้ในสนามรบในกรณีที่ล้อถูกเจาะ ล้อแบบไม่ใช้ลมจาก Polaris Defense รับประกันความทนทานที่ดีขึ้นอย่างมากเมื่อเทียบกับยางมาตรฐาน และสามารถทนต่อกระสุนขนาด 12.7 มม. ปัจจุบัน ล้อเหล่านี้มีให้ใช้งานไม่เฉพาะในรถยนต์เท่านั้น รวมถึงรุ่น Hummer เท่านั้น แต่ขณะนี้ล้อเหล่านี้กำลังได้รับการพัฒนาสำหรับรถคลาส Mraps ที่หนักกว่าด้วย
Ceradyne ยังเข้าร่วมในโครงการ Marines Personnel Carrier ร่วมกับ Lockheed Martin และ Patria บนยานพาหนะของนาวิกโยธินตาม Patria AMV ของฟินแลนด์ เป็นที่น่าสังเกตว่าในวันที่ 28 พฤศจิกายน 2555 มีการประกาศว่า Ceradyne ถูกซื้อกิจการโดย 3M Group ซึ่งจะทำให้บริษัทสามารถลงทุนใน R&D และโซลูชั่นที่เป็นนวัตกรรมใหม่ ๆ ได้มากขึ้น
การผสานการออกแบบและการป้องกันเป็นโซลูชันที่เป็นที่ต้องการอย่างมากสำหรับรถยนต์ขนาดเล็ก ที่งาน AUSA 2012 Polaris Defense ได้แสดงรถต้นแบบ Humvee พร้อมแนวคิดใหม่ที่พัฒนาขึ้นโดยความร่วมมือกับ M9 Defense ความท้าทายคือการลดน้ำหนักในขณะที่รักษาและเพิ่มระดับการป้องกัน ในการทำเช่นนี้ ทีม Polaris-M9 ได้ถอดเกราะเหนือศีรษะทั้งหมดออกเพื่อดูแนวคิดเกราะโครงสร้าง จากนั้นทุกอย่างก็ถูกถอดออกจากรถ เหลือเพียงแชสซีเปลือยเท่านั้น จากนั้นจึงวางโครงสร้างไฮบริดน้ำหนักเบา (วัสดุผสมเหล็ก) น้ำหนักเบา เกราะโครงสร้างนี้สามารถให้การป้องกันระดับ 3 ด้วยมวล 70 กก. / ตร.ม. และด้วยมวล 83 กก. / ตร.ม. ก็สามารถทนต่อกระสุนขนาด 12.7 x 99 มม. แม้ว่ากลุ่ม Polaris-M9 มั่นใจว่าทำได้ ถึงระดับ 3+ (กระสุนเจาะเกราะ 12, 7 มม.) โซลูชัน Polaris-M9 ยังช่วยปกป้องเครื่องยนต์อีกด้วย ในขณะที่รถหุ้มเกราะ Hummer มาตรฐานจะมีน้ำหนักประมาณ 6,350 กก. วิธีการแก้ปัญหาที่เสนอนี้ช่วยให้น้ำหนักลดลงเหลือ 3400 กก. เกราะโครงสร้างไฮบริดใช้วัสดุที่ไม่แปลกใหม่ ซึ่งช่วยให้ทีม Polaris-M9 สามารถพูดคุยเกี่ยวกับต้นทุนของโซลูชันใหม่ เทียบได้กับต้นทุนของโซลูชันปัจจุบัน นอกจากนี้ วัสดุนี้ถูกหล่อหลอมให้เป็นรูปทรงที่ซับซ้อน ส่งผลให้ก้นรูปตัววีไม่มีรอยต่อ เหนือสิ่งอื่นใด การได้รูปทรงที่ต้องการทำได้โดยการขึ้นรูปด้วยระบบไฮดรอลิก ซึ่งเป็นกระบวนการความเร็วสูงที่ช่วยลดต้นทุน ตามที่ทีม Polaris-M9 เทคโนโลยีนี้สามารถลดน้ำหนักได้ 40 เปอร์เซ็นต์
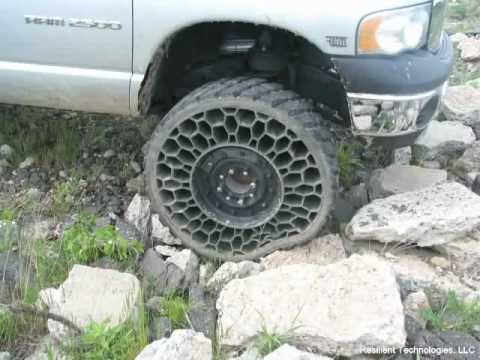
การสาธิตล้อที่ไม่ใช่นิวเมติกจาก Polaris Defense
สมการการป้องกันรวมถึงคำศัพท์อื่นที่เกี่ยวข้องโดยตรงกับความคล่องตัว - วงล้อ หลังจากการเข้าซื้อกิจการของ Resilient Technologies ขณะนี้ Polaris Defense ได้นำเสนอล้อแบบไม่ใช้ลม (NPT) การใช้ล้อเป็นหนึ่งในปัญหาด้านลอจิสติกส์ที่สำคัญที่สุดในเครื่องยนต์กังหัน และโซลูชัน NPT จะช่วยแก้ปัญหาในหลายกรณี ตามคำสั่งของหน่วยปฏิบัติการพิเศษในอัฟกานิสถาน ยางธรรมดาสามารถเดินทางได้ประมาณ 1,300 กม. ในขณะที่ล้อ NPT ที่เจาะด้วยกระสุนขนาด 12.7 มม. สามารถเดินทางได้มากกว่า 8,000 กม. ดังนั้นจึงเปลี่ยนล้ออะไหล่ออกจากห่วงโซ่อุปทานในขณะที่ปรับปรุงคุณภาพการขับขี่. มีการสร้างต้นแบบ NPT สำหรับรถยนต์ Hummer แล้ว เป้าหมายปัจจุบันคือชุดล้อ NPT สำหรับเครื่องจักรขนาด 7.7 ตัน ซึ่งเกือบเท่ากับน้ำหนักรวมของรุ่น JLTV General Purpose ตามที่ตัวแทนของบริษัท การสร้างแบบจำลองแสดงให้เห็นว่ามวลสามารถเข้าถึงได้ถึง 18 ตัน กล่าวอีกนัยหนึ่งคือ ล้อสามารถทนต่อรถคลาส Mrap ได้ เมื่อเพย์โหลดเพิ่มขึ้น เทคโนโลยีก็ยังคงเหมือนเดิม และโปรแกรมจำลองของบริษัทช่วยให้คาดการณ์ได้แม่นยำมาก สิ่งที่จะเปลี่ยนไปคือวัสดุที่ต้องปรับให้เข้ากับมวลสารซึ่งกลับไม่ปรากฏให้เห็นในอนาคต