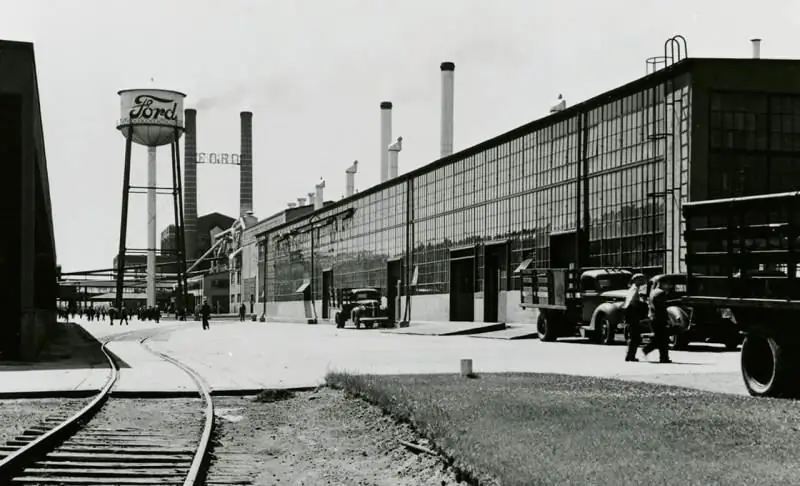
เทคโนโลยีเชิงกลยุทธ์
ก่อนที่จะทำความคุ้นเคยกับคุณสมบัติของการผลิตชุดเกราะที่โรงงานมิชิแกนฟอร์ดในดีทรอยต์ (สหรัฐอเมริกา) คุณควรอธิบายสั้น ๆ เกี่ยวกับเงื่อนไขที่อุตสาหกรรมยานเกราะถูกจัดตั้งขึ้นในสหภาพโซเวียต อย่างที่คุณทราบ ทุกอย่างเรียนรู้ได้จากการเปรียบเทียบ
การผลิตชุดเกราะในช่วงสงครามโลกครั้งที่สองเป็นหนึ่งในปัจจัยที่สำคัญที่สุดในความได้เปรียบเชิงกลยุทธ์ เมื่อเริ่มสงคราม สหภาพโซเวียตพบว่าตัวเองอยู่ในสถานะหายนะ - การผลิตอาวุธยุทโธปกรณ์ทั้งหมดกระจุกตัวอยู่ในส่วนยุโรปของประเทศ ความก้าวหน้าอย่างรวดเร็วของกองทัพเยอรมันอาจทำให้การผลิตเกราะรถถังในประเทศเป็นอัมพาตได้ ด้วยความพยายามอย่างเหลือเชื่อในการอพยพโรงงานบางส่วนไปทางทิศตะวันออกในช่วงเริ่มต้นของสงครามเท่านั้นจึงจะสามารถฟื้นฟูการผลิตชุดเกราะได้ "โรงงานหุ้มเกราะ" หลัก ได้แก่ โรงงาน Kuznetsk, Nizhny Tagil และ Magnitogorsk metallurgical
แต่เรื่องนี้ไม่ได้จำกัดอยู่เพียงแค่การถ่ายโอนการผลิตอย่างง่ายไปยังไซต์ใหม่ที่อยู่ด้านหลังแนวหน้า โรงงานแห่งใหม่ส่วนใหญ่ไม่ได้รับการดัดแปลงให้เข้ากับการหลอมเกราะของรถถัง - ก่อนสงคราม โรงงานต่างๆ ได้ทำงานตามความต้องการของผู้แทนราษฎรแห่งโลหะผสมเหล็ก Wartime ได้เพิ่มการปรับเปลี่ยนของตัวเอง ตอนนี้เตาหลอมแบบเปิดมักจะมีคนงานที่มีทักษะต่ำ มีปัญหาเฉียบพลันของการไม่มีอุปกรณ์ระบายความร้อน การกด และอุปกรณ์โลหะพิเศษ ดังนั้นการถ่ายโอนการผลิตชุดเกราะจึงมาพร้อมกับการปรับโครงสร้างเทคโนโลยีอย่างจริงจังสำหรับการถลุงเหล็กทหาร ดังนั้นจึงจำเป็นต้องปรับการผลิตให้เข้ากับเตาเผาแบบเปิดโล่งหลักขนาด 120-180 ตัน ไม่รวมกระบวนการดีออกซิเดชันแบบแพร่ การชุบแข็งของแผ่นเกราะและชิ้นส่วนเกราะต้องทำในน้ำ
ความเรียบง่ายดังกล่าวไม่สามารถส่งผลกระทบต่อคุณภาพของชุดเกราะที่ได้รับ โดยเฉพาะอย่างยิ่งกับเหล็กกล้าความแข็งสูงของถัง 8C ที่ยากที่สุดในการผลิต ตัวอย่างแรกของแผ่นเกราะในการทดสอบแสดงให้เห็นหินชนวนและการแบ่งชั้นของรอยแตกอย่างมีนัยสำคัญ ซึ่งมีแนวโน้มสูงที่จะเกิดการแตกร้าวระหว่างการเชื่อมและการยืด นอกจากนี้ การทดสอบภาคสนามยังเผยให้เห็นถึงความเปราะบางของตัวอย่างเกราะระหว่างการยิงกระสุน
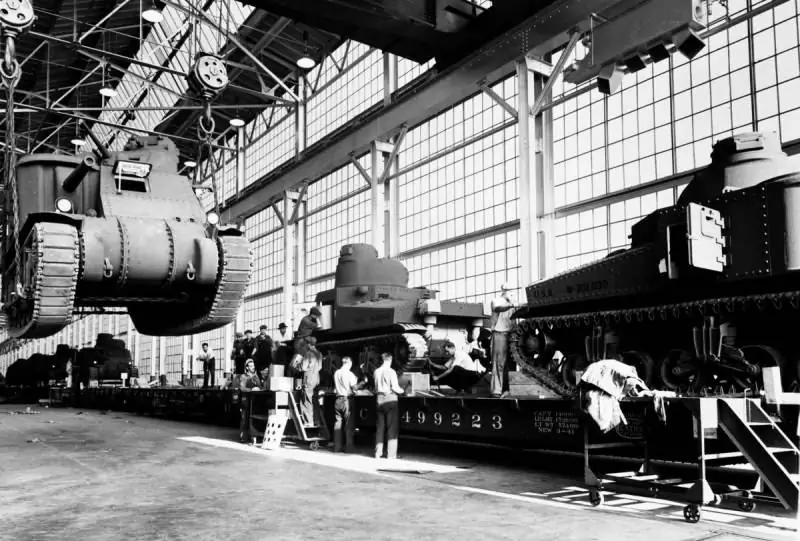
ข้อบกพร่องดังกล่าวไม่สามารถละเลยได้ และใน TsNII-48 เฉพาะทางพวกเขาได้พัฒนาการปรับปรุงจำนวนมาก อย่างแรกเลย ต่อจากนี้ไป เหล็กชุดเกราะควรจะหลอมในเตาหลอมที่อุ่นไว้เท่านั้นหลังจากถลุงเหล็กเกรด "พลเรือน" เท่านั้น เหล็กต้องต้มในอ่างหลอมแบบเปิดโล่งเป็นเวลาอย่างน้อยหนึ่งชั่วโมงครึ่งแล้วเทลงในแม่พิมพ์สี่เหลี่ยมหรือนูน นอกจากนี้ นักโลหะวิทยายังให้ความสนใจเป็นพิเศษกับปริมาณกำมะถันในเหล็กหมูดั้งเดิม (ไม่เกิน 0.06%) รวมถึงคาร์บอนและแมงกานีส ร่วมกับมาตรการอื่นๆ ทำให้สามารถปรับปรุงคุณภาพของชุดเกราะได้ โดยเฉพาะอย่างยิ่งเพื่อลดหินชนวนและชั้นของการแตกหัก
ปัญหาสำคัญคือเทคโนโลยีการรักษาความร้อนของเกราะในประเทศ พูดง่ายๆ ก็คือ การชุบแข็งและแบ่งเบาบรรเทาของแผ่นเกราะนั้นใช้เวลาและพลังงานมากเกินไป และอุปกรณ์ที่จำเป็นยังขาดอยู่ จำเป็นต้องทำให้กระบวนการง่ายขึ้น ในเรื่องนี้เราจะยกตัวอย่างทั่วไปในปี ค.ศ. 1942 นักโลหะวิทยาของ TsNII-48 สามารถลดความซับซ้อนของกระบวนการเตรียมความร้อนได้มากจนเฉพาะส่วนด้านล่างของถัง KV และ T-34 เท่านั้น ประหยัดเวลาได้ประมาณ 3230 ชั่วโมงเตาต่อ 100 ลำเรือ
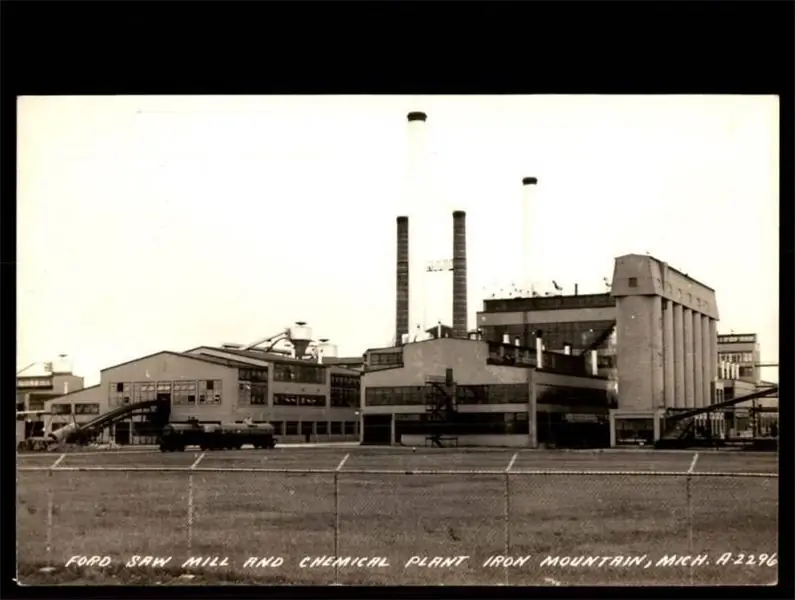
อย่างไรก็ตาม จนถึงการสิ้นสุดของสงครามในสหภาพโซเวียต เงื่อนไขสำหรับการผลิตเกราะรถถังที่มีความสำคัญเชิงกลยุทธ์นั้นยังห่างไกลจากความต้องการ ไม่สามารถพูดได้เช่นเดียวกันเกี่ยวกับอุตสาหกรรมการทหารของพันธมิตรในต่างประเทศซึ่งอาณาเขตไม่ได้รับผลกระทบจากสงครามโลกครั้งที่หนึ่ง วิศวกรโลหะวิทยาของโซเวียตต้องตรวจสอบอีกครั้งในวันที่ 26 กุมภาพันธ์ พ.ศ. 2488 72 วันก่อนชัยชนะ
ความหรูหราแบบอเมริกัน
Vasily Vladimirovich Zapariy ผู้สมัครสาขาวิทยาศาสตร์ประวัติศาสตร์ของสถาบันประวัติศาสตร์และโบราณคดีสาขา Ural ของ Russian Academy of Sciences ได้ประกาศประวัติการมาเยือนของคณะผู้แทนโซเวียตที่เยี่ยมชมโรงงานหุ้มเกราะของ Ford ในเมืองดีทรอยต์ซึ่งไม่ค่อยมีใครรู้จักมาก่อน เนื้อหาของนักวิทยาศาสตร์อิงจากรายงานของนักโลหะวิทยาของสหภาพโซเวียตเกี่ยวกับผลการเดินทางไปสหรัฐอเมริกาที่เก็บไว้ในคลังข้อมูลเศรษฐศาสตร์แห่งรัฐรัสเซีย (RGAE) ควรสังเกตว่า RGAE เป็นเพียงขุมสมบัติของเอกสารสำคัญจากยุคมหาสงครามแห่งความรักชาติที่เกี่ยวข้องกับการผลิตยุทโธปกรณ์และอุปกรณ์ทางทหาร ยังคงเป็นเพียงการเดาว่าเอกสารที่เก็บถาวรมีความลับอีกกี่ความลับในหลักฐานลับจนถึงตอนนี้
ตามคำบอกของวิศวกรที่กลับมาจากดีทรอยต์ โรงงานหุ้มเกราะของโรงงานฟอร์ดนั้นเป็นอาคารที่ประกอบด้วยสองช่วงความยาว 273 เมตร กว้าง 30 เมตร และสูงประมาณ 10 เมตร ในขณะเดียวกัน ทางร้านก็ไม่ได้ถลกเกราะ มีวัตถุประสงค์หลักสำหรับการอบชุบด้วยความร้อนและการตัดเหล็ก สิ่งนี้กระตุ้นความสนใจโดยธรรมชาติในหมู่นักโลหะวิทยาของสหภาพโซเวียต เนื่องจากปัญหาที่อธิบายข้างต้นของการผลิตยานเกราะในประเทศ โปรไฟล์การผลิตหลักของการประชุมเชิงปฏิบัติการ Ford Motors นั้นใช้เกราะหนาสูงสุด 76 มม. เหล็กแผ่นอบชุบความร้อนถูกนำมาใช้ในการเชื่อมตัวถังของยานเกราะเบาและกลางที่โรงงานอื่นๆ ในดีทรอยต์
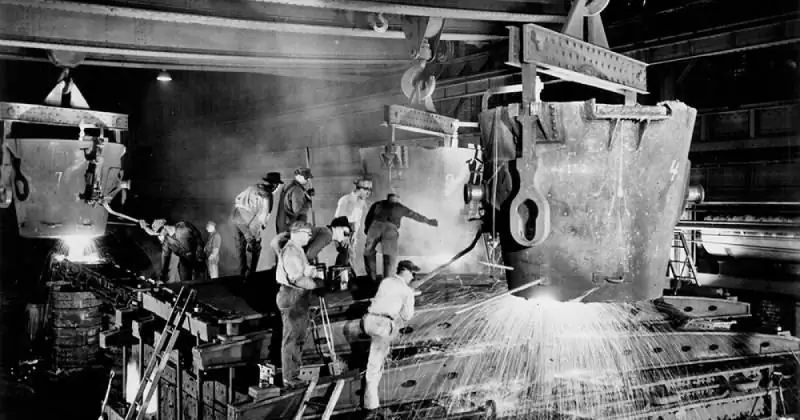
ประการแรก การใช้เครื่องจักรในกระบวนการผลิตสร้างความประทับใจให้กับการประชุมเชิงปฏิบัติการของฟอร์ด หลังจากการหลอมและกลิ้ง แผ่นเกราะถูกส่งไปยังร้านบำบัดความร้อนบนรถตักไฮดรอลิกแบบตั้งโต๊ะของ United ในทางกลับกัน รถตักก็หยิบชุดเกราะจากชานชาลารถไฟที่ตั้งอยู่ใกล้โรงงาน ในเวิร์กช็อปเอง มีเครนสะพานสองตัวที่ออกแบบมาเพื่อเคลื่อนย้ายแผ่นเกราะระหว่างการดำเนินการทางเทคโนโลยีทั้งหมด ยกเว้นกระบวนการชุบแข็ง
ในการสร้างโครงสร้างผลึกที่จำเป็นของชุดเกราะนั้น แท่นกดสองครั้งด้วยความพยายามแต่ละอัน 2,500 ตัน เตาเผาระเบียบวิธีสายพานลำเลียง 70 เมตรห้าเครื่อง และเตาหลอมสายพานลำเลียงแบบแบ่งเบาบรรเทาก๊าซ 100 เมตรห้าเครื่อง น้ำถูกส่งไปยังแท่นชุบแข็งของเกราะผ่านการทำงานของปั๊มหกตัวในคราวเดียว โดยสูบได้มากกว่า 3700 ลิตรต่อนาที ดังที่วิศวกรชาวรัสเซียเขียนไว้ ความซับซ้อนและต้นทุนของการออกแบบแท่นพิมพ์ดังกล่าว ซึ่งสามารถปั๊มและหล่อเย็นเกราะร้อนแดงพร้อมๆ กันได้นั้นเป็นสิ่งที่ห้ามปราม ในเวลาเดียวกันมีข้อสงสัยเกี่ยวกับความเหมาะสมของการใช้แท่นกดสำหรับเกราะที่มีความหนา 30-76 มม. ที่นี่ความเข้มข้นของการจ่ายน้ำเพื่อระบายความร้อนมาก่อน
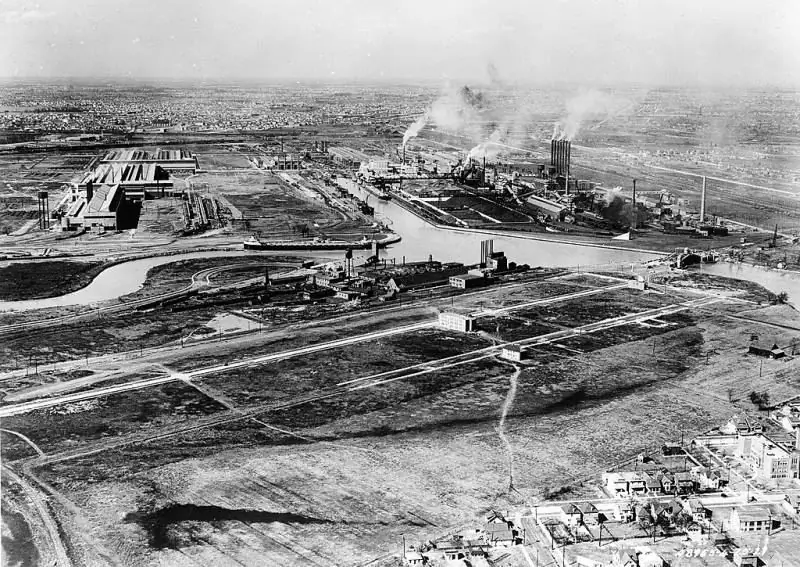
เครื่องอัดขนาด 2,500 ตันไม่ใช่เครื่องเดียวในรถหุ้มเกราะฟอร์ด เครื่องกด Toledo # 206 มีส่วนร่วมในการตัดเกราะบาง ๆ และพัฒนาแรงดัน 161 ตัน สำหรับเกราะหนากว่า 2.5 ซม. จะใช้การตัดไฟโดยเฉพาะ
ในระหว่างการเยี่ยมชมองค์กร นักโลหะวิทยาสามารถจับกระบวนการชุบแข็งเกราะกันกระสุนแบบบางได้ มันอยู่ภายใต้การกด 1,000 ตันเป็นเวลา 15 วินาทีจากนั้นส่งแผ่นเป็นเวลา 2.5 ชั่วโมงเพื่อดับที่ 900 องศาเซลเซียสและพักร้อนสี่ชั่วโมงที่ 593 องศา
วิศวกรของสหภาพโซเวียตสังเกตเห็นความมั่งคั่งทางเทคนิคทั้งหมดนี้ ไม่นับ "อุปกรณ์เสริมขนาดเล็ก" ต่างๆ เช่น เครื่องเชื่อม เครื่องกัด กรรไกร และอื่นๆ
คุณสมบัติหลักของการรักษาความร้อนของชุดเกราะคือการผลิตอย่างต่อเนื่องในเกือบทุกขั้นตอนของการแปรรูป เหล็กแผ่นอยู่ในกระบวนการเคลื่อนย้ายบนสายพานแบบลูกกลิ้งและแบบโซ่ สายพานลำเลียงถูกควบคุมจากคอนโซลกลาง ในขั้นตอนสุดท้าย แผ่นเกราะทั้งหมดได้รับการตรวจสอบระดับความแข็งของบริเนล ในกรณีนี้ ความผันผวนของพารามิเตอร์การทดสอบจากแผ่นหนึ่งไปยังอีกแผ่นหนึ่งควรน้อยที่สุด - ไม่เกิน 0.2 มม.
สิ่งที่น่าสนใจเป็นพิเศษสำหรับคณะผู้แทนโซเวียตคือเครื่องยิงระเบิดสองเครื่อง ซึ่งทำความสะอาดแผ่นเกราะเกือบหลังการใช้งานเทคโนโลยีแต่ละครั้ง ความสมบูรณ์แบบและความหรูหราเช่นนี้หาได้เฉพาะคนอเมริกันเท่านั้น ห่างไกลจากความยากลำบากของสงคราม